The stability of the paper supply chain will likely be tested during the first part of this year. The reasons for this include a decrease in the demand for uncoated paper at the tail end of 2024, along with the potential for economic tariffs on paper manufactured outside the U.S. and shipped to the states. If implemented, it’s a virtual certainty that these tariffs will challenge the paper supply chain — at least in the short-term — and result in increased prices.
This kind of volatility is problematic for brands that lean on print for their sales and marketing initiatives, but the good news is that print automation can help companies leverage the kind of print flexibility and speed that can overcome supply challenges. Let’s take a quick look at the role I believe print automation can play in faster, more flexible print.
Compatibility with virtually any substrate
The compatibility with virtually any substrate applies primarily to Landa Nanographic® Presses, but the digital, automated print nature of this type of press definitely applies when discussing the benefits of print automation in creating a more flexible print model.
With a Landa Nanographic Press, you can print on any off-the-shelf substrate, including coated and uncoated sheets and recycled paper.
The glossy, semi-glossy, or matte finishes of coated paper can be used with a variety of inks common with digital presses, including UV and specialty inks. However, because uncoated paper is rougher and more porous in nature, it’s best used with pigment inks, and the ability to transition back and forth between these ink types in successive print runs can be costly and time-consuming.
Landa Nanographic Printing Presses liberates printers from barriers inherent to traditional digital and conventional analog printing. The ability to print on any off-the-shelf substrate — coated, uncoated, treated, or untreated — helps you better adapt to and overcome the aforementioned market forces.
This enables a more flexible approach to designing and printing your project while preventing wasted time, money, and resources. Plus, this also has the potential for additional savings as you can choose the least expensive paper option that still meets your quality requirements.
The ability to facilitate multiple jobs at once
A print automation solution can print multiple jobs simultaneously on a 24/7 basis using multiple data streams. Each job can utilize different paper sizes, substrates, and inks without incurring prolonged lead times in setting up each job. What’s more, a print automation solution can leverage different levels of variable data printing and personalization based on the data available.
How does this help you create more flexible print? For transactional print, the real-time nature of print automation simplifies the process of scaling print runs on an as-needed basis. Print automation also streamlines the process of starting and pausing communications based on market forces such as new regulations or supply chain fluctuation.
Being able to produce several jobs at the same time is key for critical communications applications like the healthcare and financial services industries.
A print automation solution can integrate with your customer relationship management (CRM) software or enterprise resource planning (ERP) platform to print these kinds of documents when triggered by activity in the CRM or ERP system. These events can include when a customer submits an insurance claim, or when a patient submits an online request for financial assistance in paying a medical bill.
This kind of print flexibility and productivity helps ensure documents are printed and distributed in adherence to compliance criteria.
Quantum’s experience and expertise in print automation can help simplify and streamline your print processes regardless of the application or industry. As a strategic print partner, we’re ready to deliver the highest quality print communications quickly and efficiently.
Learn more about our print automation solutions.
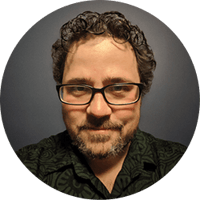
Paul Fillmore is Quantum’s Supply Chain Manager and has more than 25 years of print industry experience. Paul’s specialization is in sheet-fed printing and he has master-level experience in litho and digital print production, estimating, planning, purchasing, and process engineering.